ADL Cryogenic Oxygen Plant
Air is sucked from the atmosphere through the Air filter of the Air compressor and compressed to the desired pressure for further processing and purification to finally produce Oxygen & Nitrogen.
Over 80% of a compressor’s lifecycle cost is taken up by the energy it consumes. Moreover, the generation of compressed air accounts for more than 90% of an oxygen plant’s total electricity bill. Accordingly we now compare the advantages and disadvantages of the Air compressors.
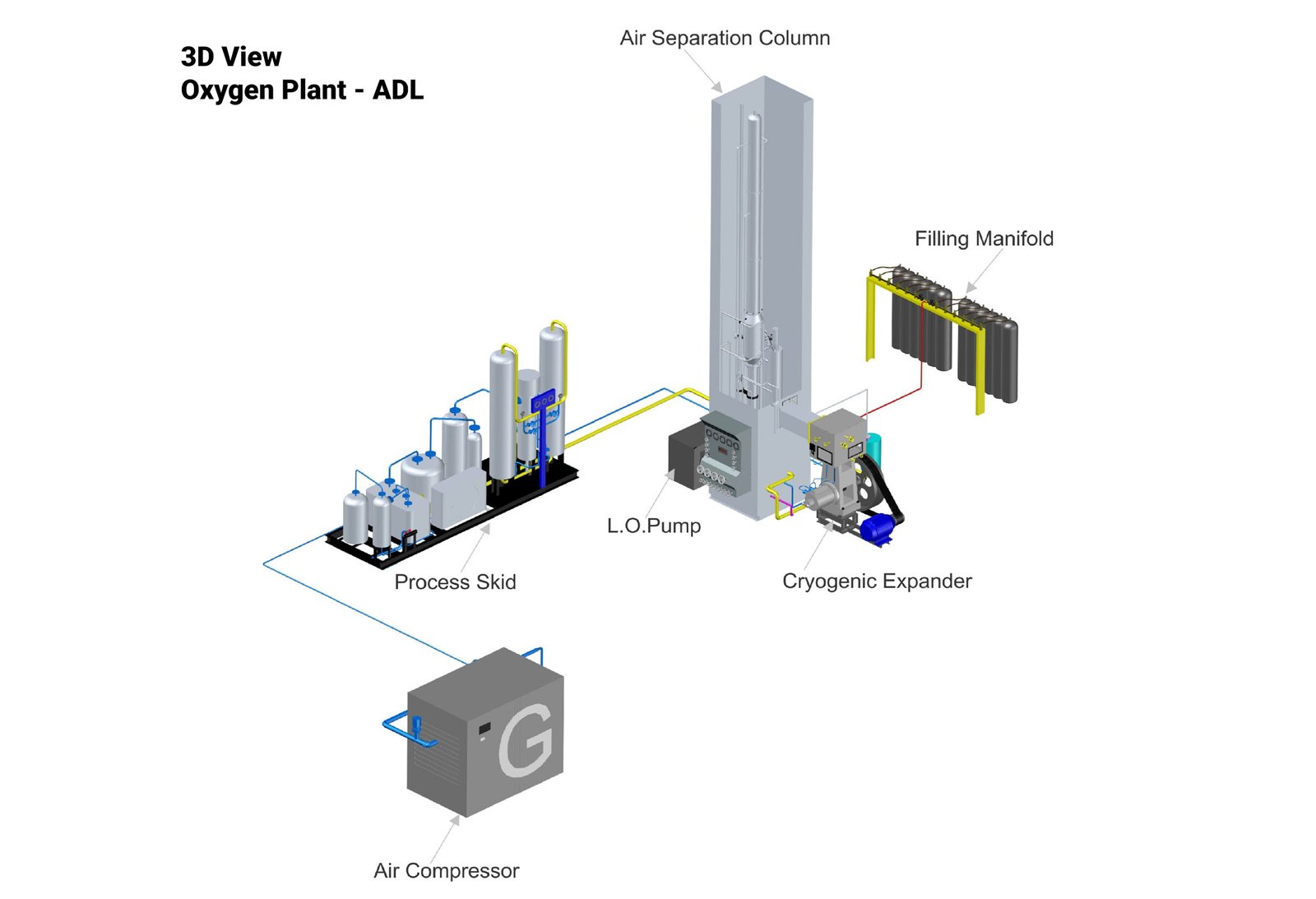
PROCESS FLOW STARTS FROM THE LEFT AT THE AIR COMPRESSOR AND ENDS ON THE EXTREME RIGHT AT THE CYLINDER FILLING STATION
Air Compressor ADL | Local Indian Piston Compressors |
---|---|
With Latest ADL Screw Compressors | With old type 4 Stage Piston reciprocating Air compressors. |
Easy floor mounting Air cooled – compact | Old oil lub ingersol air compressor piston type under breakdowns. Desined for 8 hrs duty is used for 24 hrs duty by indian suppliers |
zero maintenance !!!!! | Chinese oil piston air compressor |
No Civil Foundation is Required as it is floor mounted. | Complicated –costly concrete Foundation is required |
Installation Time: 1 Hour Very Compact design takes less space | Installation Time: 30 Days minimum * Very Bulky design takes lot of space * The complex foundation for the air compressor takes minimum 35 days additionally |
Air Cooled type- no cooling water required. | Water cooled type needs mineral water plant with minimum 30 to 100,000 Liters per day . |
Oil consumption on hourly basis as raw material is zero | Needs about 1 to 2 Liters /Hour All 4 pistons and cylinders need heavy consumption of oil |
Fully Automatic simple Operation | Fully Manual operation - old type complicated |
Low power consumption | High power consumption |
Noise Level - only 72 Dba | Noise Level is very high due to knocking of cylinders and vibration of the compressor frame |
Operational spares required for 1 Year: 1 NO. - AIR FILTER 1 NO. - OIL FILTER 1 NO. - OIL SEPARATOR (AFTER 2 YEARS) *No other operational Spares required as maintenance is virtually nil. | Operational spares required for every 4-6 months:
4 NO. - VALVE PLATE 1ST STAGE
4 NO. - VALVE PLATE 2ND STAGE
4 NO. - VALVE PLATE 3RD STAGE
4 NO. - CUSHION PLATE 1ST STAGE
4 NO. - CUSHION PLATE 2ND STAGE
4 NO. - CUSHION PLATE 3RD STAGE
4 NOS. - SPRING PLATE SUCTION 1ST STAGE
4 NOS. - SPRING PLATE SUCTION 2ND STAGE
4 NOS. - SPRING PLATE SUCTION 3RD STAGE
4 NOS. - SPRING PLATE DELIVERY 1ST STAGE
4 NOS. - SPRING PLATE DELIVERY 2ND STAGE
4 NOS. - SPRING PLATE DELIVERY 3RD STAGE
6 NOS. - RING UNDER VALVE
6 NOS. - RING UNDER VALVE COVER
4 NOS. - O’ RING
2 NOS. - VALVE PLATE
1 NO. - CUSHION PLATE
4 NOS. - SPRING FOR CUSHION PLATE SUCTION
4 NOS. - SPRING FOR VALVE PLATE SUCTION
4 NOS. - SPRING FOR CUSHION PLATE DELIVERY
4 NOS. - SPRING FOR VALVE PLATE DELIVERY
4 NOS. - RING UNDER VALVE 4TH STAGE
2 NOS. - WASHER RUBBER FOR SAFETY VALVE
2 NOS. - RING PISTON 1ST STAGE
3 NOS. - RING PISTON 2ND STAGE
6 NOS. - RING PISTON 3RD STAGE
7 NOS. - RING PISTON 4TH STAGE
|
Direct drive motor built into the Air Compressor | V Belt driven Motor drives the air compressor through rubber V belts which are manually adjusted and prone to breakage.loss of power is over 10% on account of slippage |
Noise Level less than 74 Db (Acceptable Sound) | Noise Level more than 88 Db (Need Ear Plugs) |
Local Service support is available in your country | Local Service support is not available in your country. |
MANY ADVANTAGES OF USING LOW PRESSURE ADL AIR COMPRESOR -
- Low maintenance
- Zero Breakdown
- Easy availability of spareparts
- Easy availability of service
- Low Power
- 30% saving in power bill
- No scaling due to water
- Huge saving in oil